Simple Ways to Speed Up Production Without Hiring More Staff
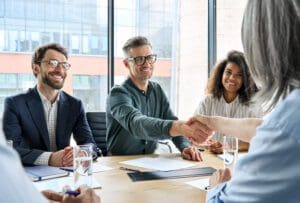
It’s not unusual for growing businesses to feel the pressure of increased demand. Orders rise, turnaround expectations tighten, and suddenly the same team has to produce more in less time.
But bringing in more people isn’t always the best solution. In many cases, smart changes in process, setup, and tools can lead to faster output, without the stress of expanding your staff. Wondering what changes?
Relax! Below are straightforward, practical ways to help your team work more efficiently while keeping the same headcount.
1. Remove the Gaps in Your Workflow
The first step is knowing where time is being lost. Look at how each task flows from start to finish. Are there long pauses between steps? Is someone always waiting on something before they can begin?
Walk through the entire process with your team. You may find that materials sit untouched for hours because the next step isn’t ready. Or tools might be shared between stations, causing delays. You don’t need to solve everything in one day, but identifying these gaps helps you know where to start.
2. Use Better Tools to Do the Same Job Faster
Old or basic tools often do the job, but they take longer. One of the simplest ways to speed things up is to switch out slow tools for ones built to move faster and more precisely.
Let’s say you’re still cutting metal by hand or using outdated gear. Switching to a plasma cutter can cut your prep time in half. These machines offer clean, accurate cuts with much less effort. One trusted manufacturer in this space builds systems that help workers cut more efficiently and reduce post-cut cleanup time, which is often just as time-consuming as the cut itself.
When the tool does its job well the first time, your team spends less time fixing mistakes or redoing work.
3. Make Repetitive Tasks Easier to Repeat
Many production jobs involve the same type of work done over and over again. If you’re setting up from scratch every time, you’re wasting hours each week.
Templates, cutting guides, saved settings, and even printed checklists help workers get started faster and with fewer errors. Whether you’re using machines or working by hand, anything that removes guesswork speeds up the job. Once a good system is in place, even new team members can follow it and stay on track.
4. Keep Work Areas Clean and Ready
Things like messy workstations might seem like a small issue, but they slow things down more than most people realize. If a worker has to stop just to find a tool or move clutter out of the way, that’s time lost.
Set up each station with exactly what’s needed—no more, no less. Use labeled bins, wall hooks, or drawer organizers. A few minutes spent setting up a clean station in the morning can save hours throughout the day. When everything is where it should be, people work faster and more confidently.
5. Train for Speed Without Rushing
Skill is important, but efficiency takes it further. If your team already knows the basics, focus next on how to do the same work more efficiently. Teach batching methods, tool shortcuts, or simple planning techniques.
This kind of training doesn’t need to be long. It can be done in 15-minute sessions. What matters is that it’s focused on saving time and improving results. Often, people aren’t using their tools or workspaces to their full potential. A little training can change that quickly.
6. Fix Problems Before They Stop You
As breakdowns hurt productivity more than anything else. One faulty tool can shut down a whole line. That’s why regular maintenance isn’t optional—it’s necessary.
Build a simple maintenance checklist. Assign it weekly. Track parts that wear out, like blades, filters, or belts. Keep a log of how often things break down. If one tool keeps slowing you down, fix it or replace it before it becomes a major problem.
7. Know Where You’re Losing Time
Use a board, spreadsheet, or basic app to track how long each step of the process takes. This doesn’t need to be high-tech. Just write down the start and end times for a few jobs each week.
Once you’ve done this for a month, you’ll have a clear picture of where time is being lost. You may be surprised to find the problem isn’t where you thought it was. From there, it’s easier to make changes that actually help.
Conclusion
Hiring more people isn’t always the answer to falling behind. In many cases, your current team can get more done with the same effort—if they have the right tools, support, and setup. From upgrading equipment to simply organizing workspaces better, these changes save time without adding stress. It’s about doing the work smarter, not harder, and the results speak for themselves.