Strengthening profit margins for UK SMEs through advanced metal finishing methods
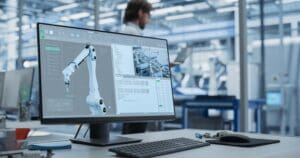
Balancing operational costs with quality production is a critical challenge for UK small and medium-sized enterprises (SMEs). Metal finishing plays a pivotal role in ensuring each component meets high standards of durability and aesthetics.
By adopting advanced finishing techniques, SMEs can enhance competitiveness while effectively managing expenses.
Many small and medium-sized enterprises (SMEs) in the UK face a challenge when balancing operational costs with the need for high-quality production. Metal finishing serves as a critical step in manufacturing, ensuring each component meets durability, safety, and visual standards. By adopting modern finishing methods, SMEs can maintain competitiveness while managing expenses effectively. For UK SMEs looking to optimize their operations, it’s essential to focus on deburring with Plasmotion. This method specifically targets unwanted burrs and sharp edges without compromising material integrity. By doing so, it enhances product quality while minimizing material loss. Reduced manual intervention also means fewer chances for human error, ultimately leading to cost savings and improved output consistency.
Improving metal finishing efficiency
Metal finishing is more than just a surface treatment; it can significantly influence product outcomes and brand reputation. Traditional processes often involve manual labour, chemical agents, and lengthy production times. These factors can create bottlenecks and higher overheads. To combat these inefficiencies, many SMEs are exploring innovative applications and investing in more streamlined, eco-friendly approaches, thereby reducing waste and improving productivity.
The transition to such innovative techniques involves understanding the current limitations of traditional methods. Often characterized by high resource consumption and potential environmental hazards, older metal finishing processes may not align with modern sustainability goals. As businesses pivot toward more efficient practices, they position themselves better in the market by aligning with contemporary consumer values focused on sustainability and quality assurance.
Financial gains from optimized processes
Optimizing metal finishing can lower production costs and bolster profit margins. By shortening lead times and reducing defects, businesses can meet tight deadlines and minimize rework. Moreover, improved finishing quality can extend product life, which instills confidence in customers and helps build repeat business. When properly managed, these practices allow SMEs to channel savings into research and development or other growth initiatives, promoting long-term sustainability.
The benefits of advanced metal finishing are not limited to cost reductions alone. Enhanced processes contribute to an SME’s ability to innovate continuously. This innovation is crucial for staying competitive in a rapidly changing marketplace where consumer preferences shift quickly. By freeing up resources through efficient operations, businesses can invest in new product development or explore additional markets.
Moreover, the possibilities of electropolishing introduce another dimension to metal finishing that many SMEs find beneficial. Electropolishing provides an ultra-smooth finish that can improve corrosion resistance and aesthetic appeal, which are vital aspects for certain industries like automotive or medical devices. Incorporating such technologies helps companies differentiate their products in crowded markets.
Key considerations for UK SMEs
Before embarking on upgrades, SMEs should assess their current equipment, workforce capabilities, and environmental compliance requirements. While any new technology demands upfront investment, choosing solutions that align with specific production goals helps maximize return on investment. For some businesses, the focus may be on precision and consistency; for others, it may be on lower emissions and safer handling protocols. By conducting a thorough cost-benefit analysis, owners can identify the right combination of technology and training for their operations.
It’s important for decision-makers within SMEs to stay informed about the latest developments in metal finishing technologies. Regularly reviewing industry reports or attending trade shows can provide valuable insights into emerging trends that could benefit their operations. Understanding these trends allows businesses to anticipate changes that might affect their market position positively or negatively.
Furthermore, collaboration with technology providers specializing in metal finishing solutions could prove advantageous. These partnerships often result in customized solutions that perfectly match an SME’s unique needs while ensuring compliance with industry standards. Through strategic alliances, companies can access cutting-edge innovations that would otherwise be beyond reach.
Deburring with Plasmotion: A strategic advantage
One emerging technique that showcases the potential of advanced metal finishing is deburring with Plasmotion. By targeting only the unwanted burrs and sharp edges, this method enhances product quality while minimizing material loss. Shorter cycle times facilitate faster turnaround, and reduced manual intervention lowers the risk of human error. For SMEs, this approach can translate to fewer production hurdles, helping to drive down costs and maintain a consistently high standard.
The application of deburring technologies such as Plasmotion aligns perfectly with modern manufacturing needs where precision is paramount. The ability to deliver consistent results without excessive waste or prolonged processing times offers significant competitive advantages over traditional methods. It positions businesses as leaders in their fields by demonstrating commitment to excellence through superior manufacturing practices.
Adopting such forward-thinking approaches requires careful planning but offers substantial rewards once implemented successfully within operational frameworks. From improving worker safety due to reduced chemical exposure risks to enhancing overall production efficiency—these advances reflect positively on both financial statements and corporate reputations alike.
For UK SMEs striving to compete in demanding markets, prioritizing metal finishing efficiencies is a tangible way to strengthen profitability and credibility. By evaluating existing workflows and adopting innovative processes—such as deburring with Plasmotion—businesses can embrace quality, sustainability, and cost-effectiveness, ensuring their continued success in a dynamic manufacturing landscape.